Botimplantaten die preoperatief 100 procent patiëntspecifiek worden ontworpen en geproduceerd. Het Limburgse Xilloc ontwikkelde daar een baanbrekende methodiek voor – met grote voordelen voor patiënt en dokter/operatieteam. ‘Dankzij jou heb ik m’n uiterlijk terug’, kreeg oprichter/ceo Maikel Beerens van een dankbare ‘klant’ te horen. cards PLM Solutions helpt Xilloc om (nog) sneller te groeien.
‘Dankzij jou heb ik m’n uiterlijk terug’
Xilloc, in augustus 2011 opgericht, is een spin-off van de universiteit en het academisch ziekenhuis van Maastricht. Met vandaag elf vaste krachten en zeven studenten legt het zich toe op het ontwerpen, maken en vermarkten van botimplantaten. Naast deze medische tak staat sinds anderhalf jaar een industriële, die 3D-geprinte producten maakt voor een groeiende klantenkring in de automotive, petrochemie, machinebouw en lucht- en ruimtevaart. Recent printte Xilloc voor het eerst succesvol een satellietonderdeel.
Ondernemer worden
Positief verschil maken in het leven van mensen met medische problemen; die droom had Maikel Beerens (nu 31) van jongs af aan. Als student werktuigbouwkunde aan de Fontys hogeschool in Eindhoven stuitte hij op lopend onderzoek naar patiëntspecifieke schedelimplantaten. ‘Ik dacht meteen: daar verbeteringen in aanbrengen wil ik voor de rest van mijn leven doen.’ In 2006 studeerde hij af op het uitontwikkelen van een methodiek om patiëntspecifieke implantaten snel en efficiënt te ontwerpen, produceren en op de markt te brengen. Hij won er de Fontys Technology Award voor de beste afstudeerscriptie mee.
Na zijn afstuderen bleef hij als onderzoeker aan de Universiteit Maastricht verbonden. Mooi en uitdagend werk, daar niet van, maar tot aan zijn pensioen een ‘Willy Wortel’ blijven zag hij toch niet zitten. ‘Ik wilde ondernemer worden, een implantatenbedrijf opzetten; punt.’ Dat ging niet zonder slag of stoot. ‘Ik had een 36-urige werkweek, was op vrijdag vrij, en zei tegen mezelf: ‘Het is me in honderd stagedagen gelukt die award te winnen; dan moet ik ook in honderd vrije vrijdagen m’n eigen bedrijf kunnen opzetten.’’ Makkelijk ging dat allerminst – ‘menigeen zou de handdoek al lang in de ring geworpen hebben’ – maar zijn droom opgeven? Nooit. Een lang verhaal kort, zomer 2011 hád Beerens z’n eigen bedrijf: Xilloc.
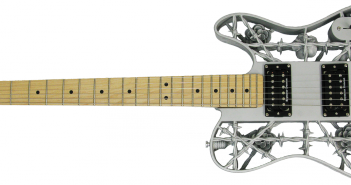
Naast wereldprimeurs als eerste patiëntspecifieke 3D-geprinte schedelimplantaat en dito onderkaak kan Maikel Beerens van Xilloc er nog één tonen: deze 3D-geprinte (aluminium) gitaar
Grote voordelen
Hij ging aan de slag met enkele mooie patenten die hij in licentie mag gebruiken. Waaronder InterFix, een unieke manier om implantaten tangentiaal op gezond bot te bevestigen. Zonder diep in details te gaan: alle schroeflocaties en -richtingen zijn, op basis van vorm en dikte van het bot van de patiënt in kwestie, preoperatief aangebracht – met instructie over de lengte van de schroef. Vergeleken met standaardimplantaten heeft dat grote voordelen: naadloze sluiting (beter resultaat, ook esthetisch); geen of minder vervolgoperaties; kortere operatieduur; minder bevestigingspunten en een kleinere kans op fouten. Mede dankzij XSuture, patent in aanvraag, dat het voor de dokter makkelijker maakt om implantaat en naastliggend weefsel te verbinden.
Minder belastend en een beter resultaat voor de patiënt, minder kopzorg en tijdwinst voor de behandelende dokter. Beerens: ‘Onze aanpak neemt artsen veel werk uit handen. Zij hoeven alleen nog hun input te geven in ons systeem, de rest regelen wij. Omdat wij de hele workflow geoptimaliseerd hebben, gaan zij beter voorbereid en relaxter de ok in.’ Dat werkt zo: de dokter stuurt een ct-scan, die aan bepaalde (resolutie)voorwaarden voldoet, en andere parameters naar de Xilloc-webshop. Met geavanceerde CAE-software vertaalt Xilloc die data in een patiëntspecifiek implantaat, dat in overleg al dan niet bijgesteld wordt. Vervolgens zet Xilloc CAM-software in voor de beste productieaanpak. Daarna maken en uitleveren, klaar is Kees.
Nieuwe uitdagingen
Schedelplaten, oogkasbodems, jukbeenderen, kaakstukken; Xilloc kan die maken. ‘Tot voor kort lag onze focus op hoofd/hals, maar we zakken voorzichtig af naar extremiteiten als pols-, sleutelbeen- en scheenbeenimplantaten. Met nieuwe uitdagingen: vaak standaardimplantaten, maar wel met een klantspecifieke planning.’ De materialen waaruit Xilloc al die spullen maakt zijn patiëntbepaald. ‘We zijn sterk in 3D-printen van polymeren, metalen – als titanium of aluminium – en keramiek. Titanium leent zich prima voor 3D-printing: daarmee kun je heel complexe rasterstructuren opbouwen waarin bot kan groeien. Of met een laag gewicht, wat voor veel industriële klanten zwaar weegt. Maar voor een schedelimplantaat is metaal geen optie: te koud op wintersport, te heet op het strand. Dus dan passen we polymeren toe. En in weer andere gevallen kiezen we voor hybride: een combinatie van 3D-printen en traditioneel frezen.’
Xilloc beschikt daartoe over een state-of-the-art machinepark, met onder meer vier industriële 3D-printers (merk OES) en een grote cnc-freesbank (DMG) waarop 3D-geprinte implantaten worden nabewerkt (voor een glad oppervlak) en schroefdraad (in 3D nog niet goed mogelijk) wordt gedraaid. Die spullen komen ook van pas voor Xilloc Industrial, meldt Beerens: ‘Een klant kwam met een product dat op de conventionele wijze gemaakt 1,4 kilo weegt. Hij wilde dat lichter. Wij bedachten op basis van 3D-printing een meer organische structuur die op 800 gram uitkwam. Daar winnen we klanten mee.’ Dat blijkt: Xilloc groeit gestaag. ‘Onze strategie is eerst een solide basis in West-Europa opbouwen en daarna de vleugels wereldwijd uitslaan. Langzamerhand gaan we daar naartoe: we zitten in een voortraject met de FDA (Amerikaanse Food & Drug Administration, red.) om daar de markt op te gaan.’
Minder tussenstappen
Om die groei te stutten, heeft Xilloc de banden met cards PLM Solutions aangehaald. Paulus van Dreumel, account manager bij cards: ‘Xilloc maakt al gebruik van de Siemens PLM NX-software. Daarmee halen ze de geometrie binnen en bewerken die waar nodig. Daar komt bij dat Siemens onlangs een partnership is aangegaan met EOS, leverancier van hun 3D-printmachines. Die software wordt straks geïntegreerd in de NX-suite. Dan kun je vanuit NX niet alleen de geometrie bekijken, maar ook hoe al die laagjes daadwerkelijk fysiek worden opgebouwd in de machine. Zo kom je zinnige dingen te weten over die opbouw, het support-materiaal dat de geometrie ondersteunt, de warmtegeleiding, enzovoort. Dat scheelt heel veel tussenstappen. Verder stuurt Xilloc met onze software hun nabewerkingsmachine aan. Aan 3D-geprinte producten moet je vaak nog een stukje klassieke cnc-nabewerking doen. Dat doen ze met NX CAD/CAM-software.’
Maikel Beerens heeft daar hoge verwachtingen van. ‘Software die kan voorspellen wat er in een geometrie gebeurt, daar schieten we echt veel mee op. Vandaag de dag is een 3D-printer een black box. Gelukkig hebben wij inmiddels zoveel ervaring dat we bijna zeker weten dat we het goed doen zoals we het doen. Maar dan nog kan het wel eens verkeerd gaan. cards PLM Solutions gaat ons helpen dat te voorkomen.’ De mogelijkheden die NX CAD/CAM biedt, noemt hij de holy grail. ‘Onze producten komen in stappen tot stand – en elke stap vergt complexe vertaalslagen in je files. Met NX CAD/CAM worden die in één keer overbodig. Dezelfde file voor je 3D-printer en freesbank, briljant.’
Anderhalf jaar geleden verkaste Xilloc van Maastricht naar de Chemelot Campus in Geleen. ‘Van vijf mensen op 100 m2 gingen we naar elf op 600 m2. Volgend jaar gaan we hier vlakbij naar een nieuw pand en hebben we 1.100 m2 tot onze beschikking, waarmee we de grootste professionele industriële 3D-printfabriek van Nederland zijn .’